When you first start out with 3D Printing, you’re likely to print almost exclusively PLA – and for good reason.
PLA is easy to use, affordable, and great for maybe 80% of the things you’d want to print as a beginner.
However, as you get more skilled both in 3D Printing and in understanding what types of things you CAN print, you’ll inevitably want to try more versatile, tough, or durable materials.
Well, stick around, because in this article, I’m going to give you a quick guide as to which filaments are best for what types of projects, and how to choose which one to use for YOUR next project.
Let’s dive in!
What Are The Different 3D Printing Filament Types?
Without further ado, here is the list of my most used 3D printing filaments and the difference between them:
PLA
First, let’s start out with PLA, or polylactic acid – and if you feel like you’re already a PLA pro, feel free to skip ahead.
Polylactic acid has become an incredibly popular polymer, not just in 3D printing, but in many other uses, because it’s easy to produce from renewable resources. In fact, in 2021, PLA had the highest consumption of any bioplastic in the world.
PLA is probably best known for two things: it’s low melting point and it’s high rigidity.
In fact, while many people erroneously believe that materials like ASA, PETG, or ABS – which we’ll get into in a minute – are stronger than PLA, the fact of the matter is, as shown in Stefan from CNC Kitchen’s rigorous testing, basic PLA is by far the strongest material in a hook test, as well as in a 3-point bending test – meaning it’s also the most rigid.

With that said, PLA’s extreme rigidity also comes with a tradeoff, and we see from Stefan’s testing that the impact strength of PLA is much less than other materials.
Of course, there are materials out there like this so-called PLA+ or “Tough” PLA, which add impact resistance or a bit of flexibility depending on which brand you go with.
I generally go by `the motto that a tiger doesn’t change it’s stripes, and if you can print another material like the ones we’re about to talk about for the suitable application, you should.
Finally, let’s address that other well-known criteria of PLA, and the one that makes it so popular for 3D printing: it’s low melting point.
PLA doesn’t like heat, and while you might think to yourself that it’s melting point is high enough – somewhere around 190 degrees celsius for actually printing it, the fact is that it will begin to deform at much lower temperatures.
I’ve had PLA parts deform in a printer cabinet that never exceeded 45 degrees celsius. What’s more, while PLA is surprisingly chemical-resistant, it is known to not respond well to UV or direct sunlight. Finally, it also is known to deform over time if exposed to constant strain.

So what’s the verdict: What should we use PLA for?
First of all, because of the wide availability of colors and styles, ranging from standard colors, to matte ones like a Bambu Lab spool, silk, rainbows, and even co-extrusions and more, PLA is the reigning champion for anything decorative such as statues, toys, and so on.
But it’s not just limited to that.
You should also consider PLA for any type of indoor functional parts which will not be exposed to temperatures above ambient or excessive and prolonged force.
That means that while PLA is probably not a good fit for your PC fan ducting, it’s great for things like your honeycomb wall, gridfinity, shelf brackets, or even a compost bin. I’ve even used PLA for my trash bins at home, and it works great.
TPU
Inevitably, in your 3D Printing journey, you’re going to decide that you want to print something flexible, and when you do, TPU is most likely where you’re going to end up.
Though there are many flexible plastics out there, for a number of reasons way above my pay grade, TPU is generally the only plastic you find used in 3D Printing.
TPU comes in a number of different hardness ratings, with the lower number A rating being softer than the higher number. And generally speaking, the harder, the easier it will be to print.
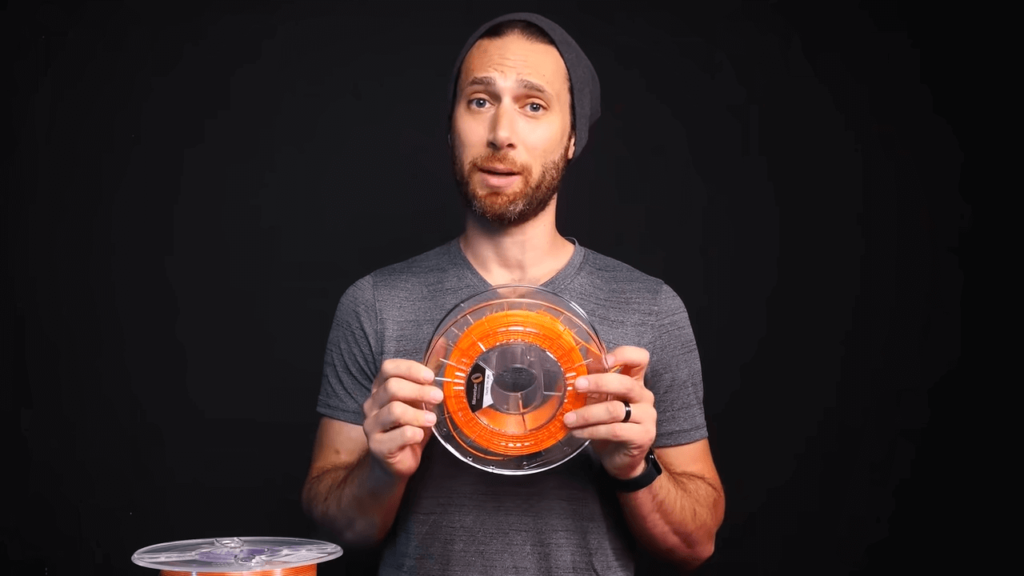
This is because softer materials can be extremely tricky to extrude – especially if you’re not using a direct drive extruder. I mean, just imagine pushing a wet noodle through a drinking straw. Not fun, right?
In any case, there isn’t too much to say here. If you need a flexible print, like a seal on a box, or something that’s going to absorb impact like a door stopper or a table corner, TPU is going to be the filament of choice. Nuff said!
PETG
Up next, let’s talk about PETG, or Polyethylene Terephthalate Glycol.
This is often seen as a natural “next step” material to PLA, and offered by many filament manufacturers as a tougher alternative to PLA, with similar printability.
But I’m going to just go ahead and say something controversial: I don’t believe that PETG deserves the popularity it enjoys.
First of all, if we once again reference Stefan’s fantastic test data, we see that PETG doesn’t actually excel at anything in particular when compared to other materials:

What’s more, while PETG does have higher heat resistance, and significantly better UV resistance, it pales in comparison to that of ASA.
What’s more, PETG suffers from a number of “quality of life” issues, including the fact that it sticks too well to most beds and can damage your print surface, the fact that it sticks to nozzles and “boogers” up, and the fact that it’s extremely hygroscopic, and must be dried thoroughly before printing.
Oh, and on top of that, it’s also very slow to melt, meaning that you cannot use PETG for any of the “high speed” printing that is becoming so much more common.
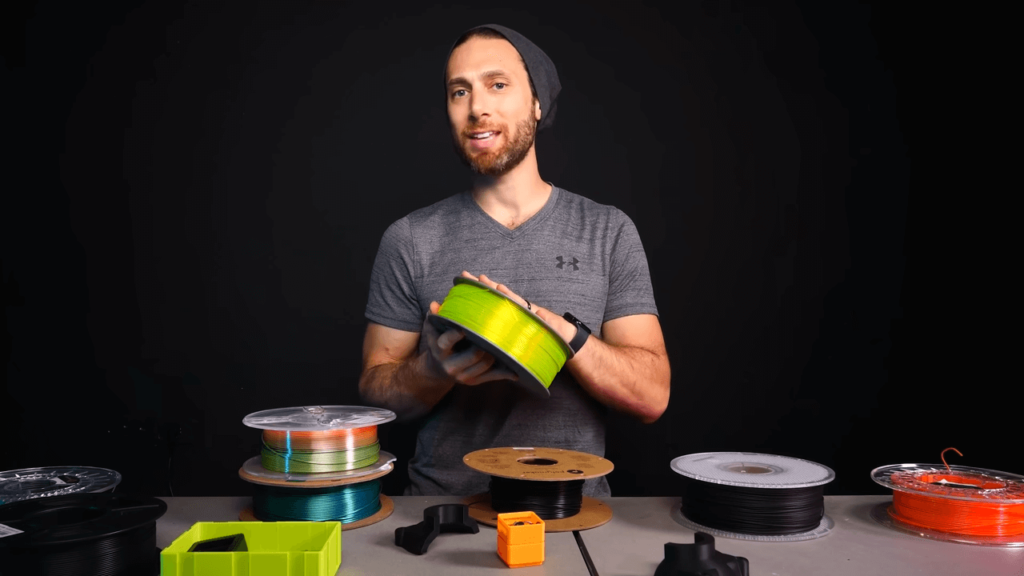
All in all, I’m just going to say it: PETG is a pain in the butt!
So why, then, is PETG so popular?
Well, it’s actually quite simple: it’s historically been easier to print than ABS or ASA.
You see, while PETG has all these things counting against it, it has one MAJOR thing going for it: it can be printed on an open printer without needing to worry about things like warping.
And with the previous generation of open, slow, bedslinger designs, many of the “downsides,” like being too sticky or not flowing as fast as, say, ABS, were non-issues.
However, today, in 2023, with more and more people having enclosed, fast printers, PETG is really starting to show it’s limits.
So much so that some companies, such as Bambu Lab, aren’t even offering it to their customers except in it’s carbon-fiber variant: .
So what, then, should you avoid PETG altogether for your projects? Well, not quite.
You see, as I mentioned before, PETG is superior to PLA in terms of heat and UV resistance, and when compared to something like ASA, it’s often significantly cheaper – though still more expensive than PLA or ABS in many cases.
Plus, PETG offers a great mix of strength and flexibility, and it has more “give” than other materials. It also comes in lots of colors, and is better for “translucent” colors that don’t cloud – I mean, just look at this gorgeous translucent neon color by Fillamentum.
Finally, it really is much more warp resistant than even ASA – which is touted for it’s warp-resistance. So if you don’t yet have an enclosed printer, PETG is going to be one of your best options for functional parts that need to withstand either moderate heat, UV, or sustained strain.
These days, I only think of PETG when I need a material to have some “give.” But in the past, I’ve used PETG for things like this vertical planter, RepRack brackets, fan ducts, replacement light diffusers, and even a softbox for my video light, which needs to flex a little bit to clip on.
However, if you do have an enclosed printer, in my opinion, you’re better off looking into one of the next two materials.
ABS
And, here we go, we’ve gotten to the part of the article that I’ve been dreading – the part where I try to pronounce the proper name for ABS: Acrylonitrile Butadiene Styrene.
You may not realize it, but ABS is probably the most commonly used plastic in your day-to-day life, used in everything from Lego blocks to automotive parts and much, much more.
This is because ABS offers a whole host of benefits as compared to other plastics.
It’s got a great balance of impact resistance, toughness, and rigidity, particularly if you use some of the “ABS+” variants that are available out there.
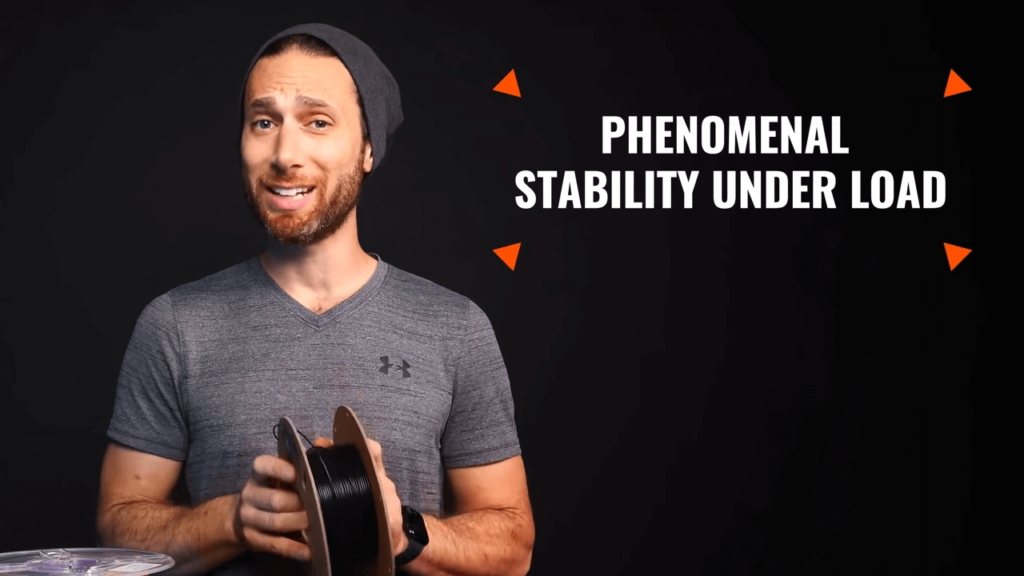
ABS also offers phenomenal stability under load, making it the plastic of choice for any functional parts that will be under sustained stress, particularly in reasonably warm conditions.
This, for example, is why ABS – even just this basic roll of the no-frills kind from Polymaker – is the recommended material for the printed components of Voron 3D printers.
ABS is also great because it allows for vapor smoothing, in case you need to make layer lines disappear.
Finally, ABS is notoriously quick at melting and flowing, which is one of the main reasons it is the standard in injection molding. So, if you’re looking to print things fast, ABS is a great contender!
With that said, there are some downsides to ABS, as with all materials.
First of all, it warps. A lot.
In fact, most people would agree that your standard ABS cannot be printed without an enclosed printer, and even still, ABS is best printed in a very warm environment, even if an actively heated chamber isn’t necessary.
As if warping weren’t enough of a reason to only print ABS enclosed, there are also the fumes. Printing ABS stinks, and can emit harmful VOCs that you don’t want to be breathing.
So not only should you print it enclosed, but you’ll also want some type of carbon filter in the enclosure, too.
When I first started using ABS, on my Prusa MK3S+ in a custom enclosure, I had nothing but difficulty, and I swore that I would never buy another roll again.
However, over time, as I migrated to more enclosed printers with smaller enclosures that could actually heat up the build volume properly, I have discovered that ABS is actually easier to print than even PLA or PETG – unless I remove the panels from my printers to allow for better cooling of those materials.
As mentioned before, I like to use ABS for anything that will be under sustained load, anything that I need vapor-smoothed, or anything that needs to sustain high heat, without necessarily being exposed to UV radiation.
Examples include the brackets for mounting a camera in my enclosure, filament spool rollers, various brackets for electronics that will be exposed to heat, and more.
Yes, ABS is sort of a non-starter for open printers, but fear not, because we still have yet to cover:
ASA
Acrylonitrile Sytrene Acrylate, or ASA, is in many ways very similar to ABS.
In fact, I like to think of it as the new and improved ABS.
While it is generally much more expensive than ABS, it offers improvements in virtually every one of it’s predecessor’s shortcomings.

First of all, it can be printed without an enclosure, as long as there are no drafts.
Second, it has much higher UV resistance. Third, it is even more resistant to environmental stress cracking, long-term heat, and chemicals. It can also be vapor-smoothed.
And then, there’s the smell. High-quality ASA has significantly fewer fumes, and while I haven’t done any scientific testing on VOCs emitted, I can definitely share that anecdotally, I get far fewer headaches when printing it out in the open. It even has lower shrinkage, making it easier to get perfect dimensions.
Unfortunately, it’s not all sunshine and rainbows with ASA.
First, as I mentioned, there’s the price – often costing 50-100% more than the cheapest of ABS’s:
Then, there’s availability: whereas ABS is available from dozens of manufacturers in practically every color imaginable, ASA is much less available from far fewer manufacturers.
Finally, there’s bed adhesion.
Personally, I have always had an awful time getting most brands of ASA to stick to any print surface, ranging from glass to PEI, and I inevitably end up using mountains of hair spray, glue stick, and more just to get my prints to stick.
What, then, should you use ASA for? Well, obviously, anything that you plan to put outdoors is a fantastic candidate for ASA.
Additionally, any of the uses mentioned above for ABS are going to be even stronger, more heat resistant, and more durable if printed in ASA – plus, if you’re using an open design printer, then you should definitely skip right over ABS altogether.
Personally, because I have a number of enclosed printers, these days I’m choosing to save a little bit of money and buy ABS more often than I buy ASA, unless I need the UV resistance, such as something I’m specifically printing for outdoors.
ASA is just too much of a pain to get to stick, plus, I generally don’t need the added mechanical durability that it offers – or if I do, there are other materials or copolymers I can choose from.
Unfortunately, we don’t have time in this article to cover more different materials – things like Nylon, Polycarbonate, or Carbon Fiber blends, but if you’d like to see me do a video explaining when you should use THOSE materials, please drop me a comment and let me know.
That’s all for now, but I’ll see all of you on the next layer.