These 3D Prints are garbage.
And no, I’m not talking about the print quality – because they’re actually pretty decent.
I’m talking about the fact that they are literally made from repurposed municipal waste.
No, I don’t mean that someone just yanked the plastic out of the dumpster to make filament.
I mean that this filament – made with an innovative compound called UBQ – is literally made of mostly garbage. Banana peels, diapers, and all.
Now, we’re going to get into how it prints and all of that in a little bit, but first, I’m sure you have a lot of questions about the material itself.
Introducing UBQ Materials
To start, I have got the chance to interview in-person the VP of Marketing at UBQ Materials, Liat Arad.
You can watch the full interview here:
Plastics App UBQ Filament Review
Where were we? Oh, yeah, turning those refined UBQ pellets into actual 3D Printing filament you and I can use.
For that, UBQ partnered with another company here in Israel, Plastics App, that specializes in developing unique and tailor-made polymers for various applications and industries.
Plastics App, in turn, took the finished UBQ additive, and created a few different unique compounds for making it 3D Printable. They were kind enough to send me one of them, this roll of “EZ-Q”(see below), designed to be as easily printable as possible.
Though the exact composition is a closely-guarded secret, Plastics App assured me that this roll is still significantly composed of UBQ, as opposed to virgin material, and that their goal in developing it was either carbon neutrality or even a negative carbon footprint.
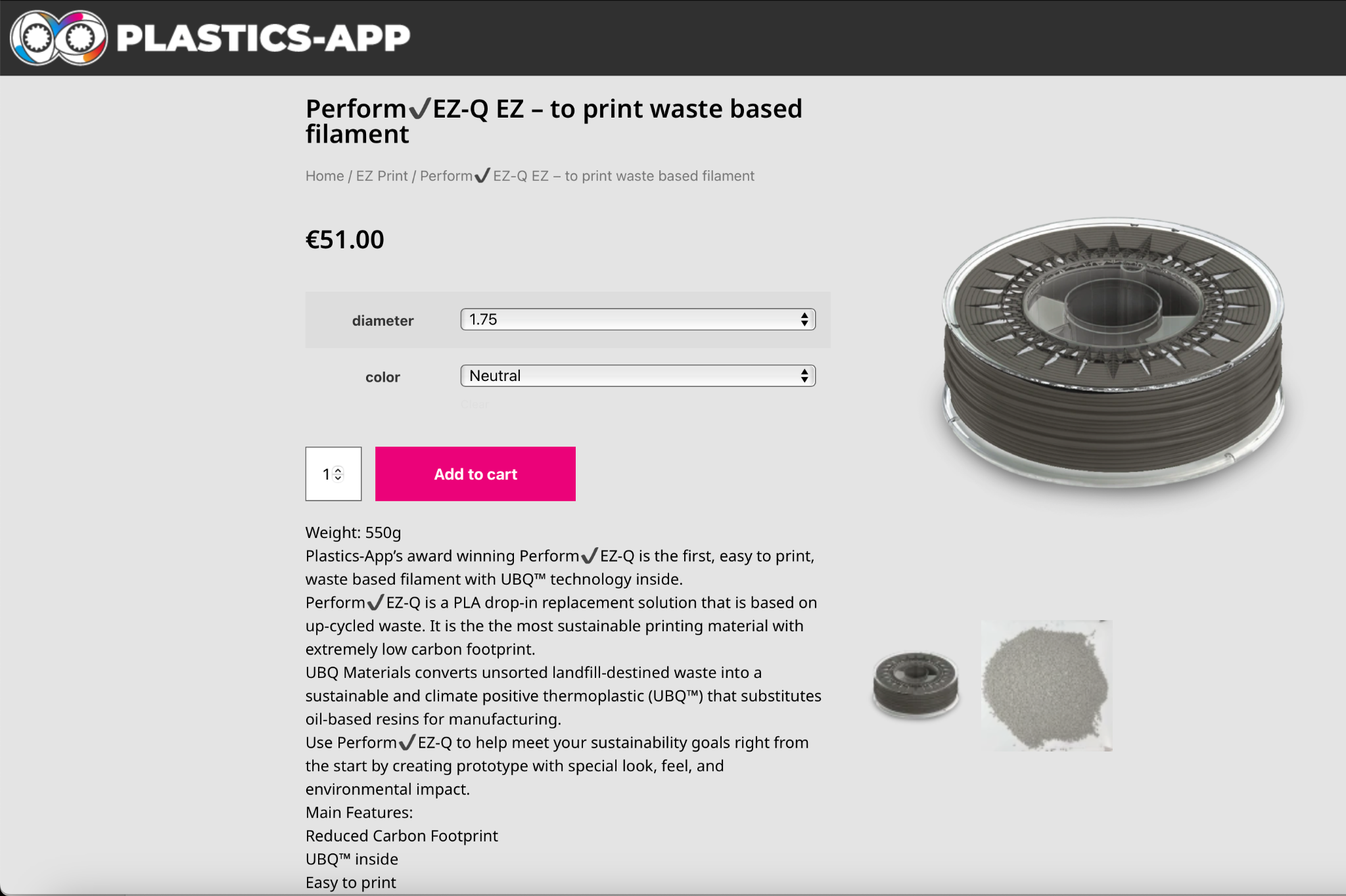
The bottom line? This filament is basically made of trash. Highly refined, technological miracle trash, but trash nonetheless.
But does it PRINT like Trash? I had my doubts. Especially because, just trying to insert it into the printer, it proved to be incredibly brittle – akin to a woodfill filament.
And yet, I was pretty blown away by the printability – and I was even able to print with it on my super-fast Bambu Lab X1 Carbon.
To be clear, because of the UBQ additive, you do need to print this material with a wear-resistant nozzle of at least 0.6mm in diameter, such as the new GammaMaster nozzle that Slice Engineering was kind enough to send over, but otherwise, it pretty much prints like normal.
After seeing Zach Freedman’s “curved filaments” series, I honestly expected this stuff to be much harder to print with, but in all truth, all it took was a generous amount of drying the filament out – much more than I would with PLA, for example – and then dialing in settings like retraction and heat.
Surprisingly, despite it having so much “additive” in it, it prints best at 190 degrees celsius, and when it’s properly dry, the prints are almost indistinguishable from Matte PLA, or a fiber-filled PLA like this wood one.
Though admittedly, for some of these parts, I got lazy and didn’t dry the filament out, so excuse some of that stringing. And, because I know you’re wondering, no, there isn’t a nasty smell when printing it, though there also isn’t that “sweet” smell that virgin PLA emits, either.
Material Strength and Pricing
Now, I know that you’re probably ALSO curious about the material’s strength, and so while this isn’t CNC Kitchen – I did go ahead and buy some test equipment to see just how strong this stuff really was.
And while I did use Stefan’s exact settings for printing these hooks out, let’s just say that my test methods were less than scientific. And, because of time constraints, I admittedly had a very small sample size.
From my very limited testing, though, the environmental benefits of this material definitely come at a cost, and my test samples broke at about ¼ the load of Stefan’s PLA samples. I’m sure that with more tweaking, I could get better results, but there’s no two ways about it: the strength of this material is a bit disappointing, and may limit it’s practical application. Another bit of disappointing news is the price: the roll I tested sells for €51 for a 550g spool, making this one of the more expensive filaments you can buy – though I’m sure economies of scale could bring those prices down if it were mass produced.
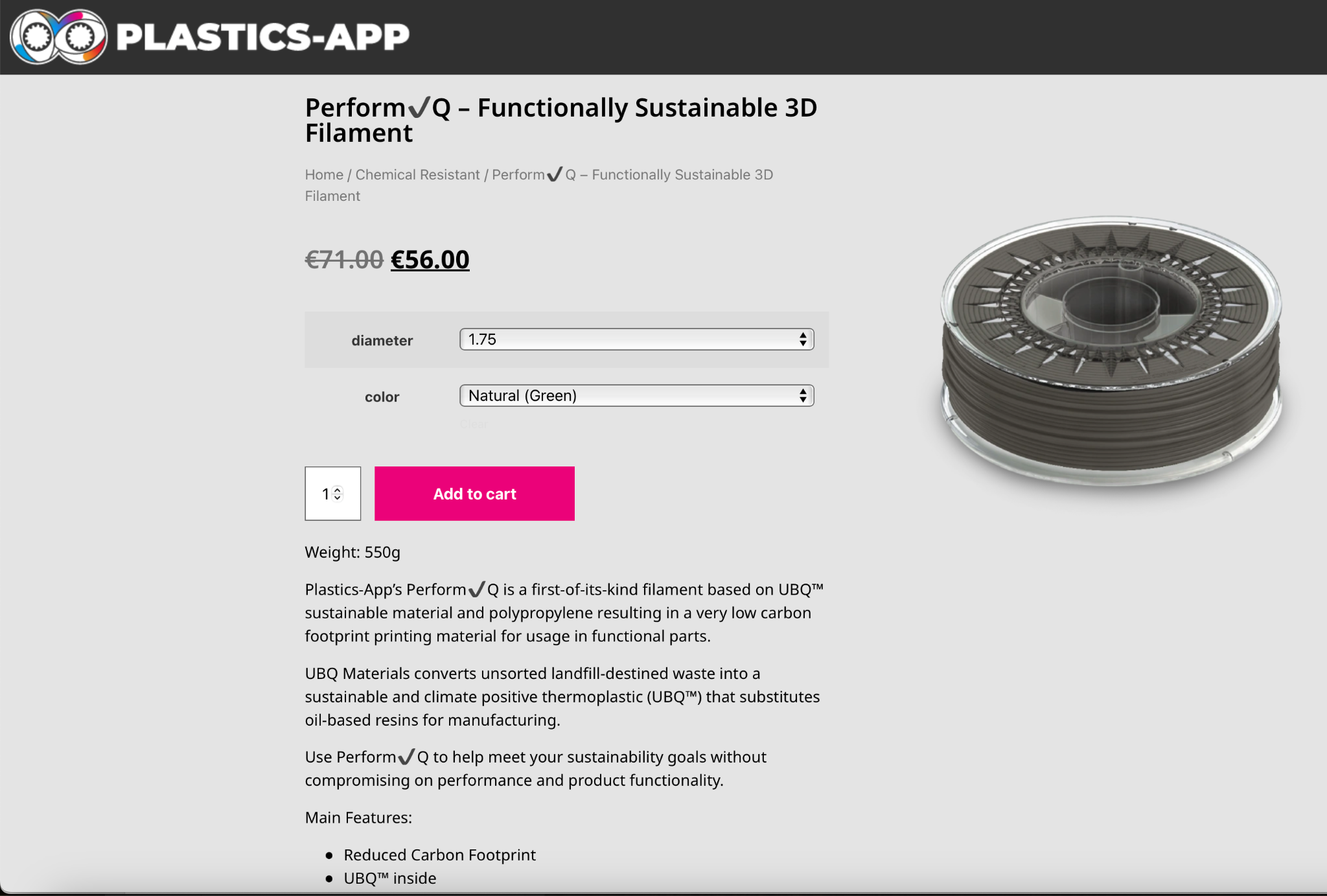
Nonetheless, I was really happy to hear when Yanir, CEO of Plastics App, told that they have still had a lot of interest from all different kinds of industrial customers, including automotive manufacturers, lighting and home goods designers, architecture firms, and more for this filament.
Which kind of made me realize; sometimes, especially in the context of a business, strength, or even aesthetics, are not what you’re optimizing for.
As consumers, we’re almost always looking for the strongest, best looking part – at the lowest possible cost. But imagine if you’re an automotive manufacturer, designer, or architect designing tens, hundreds, or thousands of prototypes that you know are inevitably going to be scrapped.
In that case, you’d either want to recycle the material – which isn’t always possible – or, you’d want to use a material that you know had a significantly lower carbon footprint, so that the overall environmental impact of your business is effectively lowered.
And if your business, like so many major companies such as Apple, has the goal of becoming 100% carbon neutral or even carbon negative, integrating this material into your design process could be a big part of that strategy – a strategy which has other benefits, such as increasing your stock price, or bringing you in line with regulations.
But don’t get me wrong; I don’t think that this filament is only useful for things you’re planning to throw away.
I’m quite sure that although the strength isn’t nearly as good as virgin PLA, this material – with it’s earthy, natural look – could be used in all kinds of finished products, either inside the product, or visibly.
I got to be honest, I kind of like the textured matte finish. And if you’re selling to environmentally conscious consumers, I think the story behind this filament can actually be a major selling point.
And keep in mind: 3D Printing is just one, very niche application of UBQ’s technology. When used in other manufacturing processes such as injection molding, UBQ is already being used major multinational corporations – companies like McDonalds, Mercedes Benz, and more – in finished products that consumers are using every day.
Conclusion
The bottom line? This filament may be quite expensive – and quite weak compared to virgin materials – but it represents a really awesome application of a cutting-edge technology for solving one of the most pressing problems facing humanity today: what to do with all of our garbage.
While I don’t think you’re going to see rolls of UBQ infused filament on the shelves at Microcenter any time soon, I DO think it’s awesome that industrial customers have the option to use this type of material in their prototyping and production processes, and I certainly hope to see more trash skipping the landfill and ending up in more of the products I use every day.
But what do all of YOU think? Could you ever see yourself printing with garbage, if the prices were similar to a normal roll of filament? Could you see the company you work at using this as part of a bigger strategy to reduce carbon emissions? And most importantly, are you interested in seeing MORE content like this about 3D Printing innovations?
Let me know in the comments section below!